Cross-project workshop on the topic of securing and maintaining raw materials with foundry dust
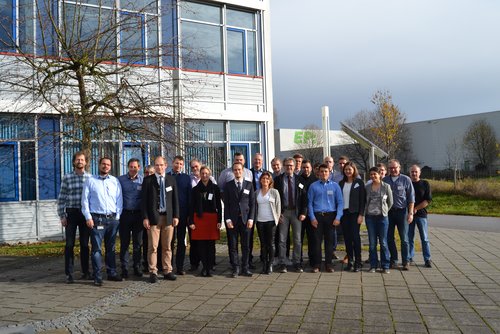
Augsburg, 29 January 2020
As part of the ForCYCLE II project on efficient use of dust from foundries, which is funded by the Bavarian State Ministry of the Environment and Consumer Protection (Bayerischen Staatsministerium für Umwelt und Verbraucherschutz) and carried out by the University of Augsburg, bifa Umweltinstitut and other partners in practice, a creative workshop was held at bifa Umweltinstitut in Augsburg with numerous representatives of industry and science.
In the workshop, initial approaches to solving the following issues were worked up together. Which treatment methods are ecologically and economically possible for such filter dust and what are the potential uses for the treated material flows?
Dust produced during the casting of iron is drawn off via exhaust extraction systems and is separated out in filters. The dust can contain contaminant fractions and have a high proportion of dissolved carbon; therefore, in general, simple disposal routes are not possible. The dust is often placed in mine filler, but in some cases, it can also be necessary to dispose of it on a hazardous waste landfill site. Which recovery route is possible depends on the respective properties of dust. These not only include the chemical composition (content of main components and trace elements), but also the physical properties (bulk density and particle size).
In many cases, recovery is simplified if the material flows are not classified as dangerous waste. Separating out contaminants is therefore frequently a requirement for successful reuse.
Thanks to the participation of representatives of different branches of industry as possible users, research and the participating foundries, a lively discussion resulted at the workshop. Thus, the possibility of enriching constituents and the extraction of recoverables through dry mechanical or wet mechanical process technology was considered. Another interesting point of discussion was treatment using chemical processes. In this way, the dust is to be optimised for different potential uses, while complying with limit values and specifications. For this topic, very interesting approaches to separating out heavy metals from the dust were presented by the participants from research and development. Further, different recovery routes were discussed for foundry dust that already has a high iron fraction: To what extent can it be recovered efficiently or what parameters must be used to achieve this? For example, can it be used in the brick or cement industry? Here the discussion mainly concentrated on the impurities in the dust and what potential treatment could remove them. During the rounds of discussions, innovative ideas were developed, which are to be followed up. To return the material flows to the foundries, there is also the approach of incorporating dust in existing alloy mouldings. Here too, the critical heavy metals must be extracted from the dust before they can be processed further. Is there other potential in foundries, which is not used? Discussion of this topic was also lively.
The workshop was attended by the foundries involved in the project (Giesserei Heunisch GmbH, Kemptener Eisengießerei Adam Hönig AG and Trompetter Guss GmbH Co. KG), as well as the SME project partners AKW Apparate+Verfahren GmbH and GPS SIC Keßl GmbH u. Co. KG. The treatment and user industry was represented by Lober GmbH & Co. Abfallentsorgungs-KG and Fabb-IT UG, as well as MAN Augsburg. Representatives of the following research institutes took part: LMU Department for Geo and Environmental Sciences, Fraunhofer Research Institution for Material, Recycling and Resource Strategies - IWKS, and the University of Augsburg’s Institute of Materials Resource Management und bifa Umweltinstitut GmbH also took part.
The project is being funded by the Bavarian State Ministry of the Environment and Consumer Protection.