European Eco-Solar Factory project completed
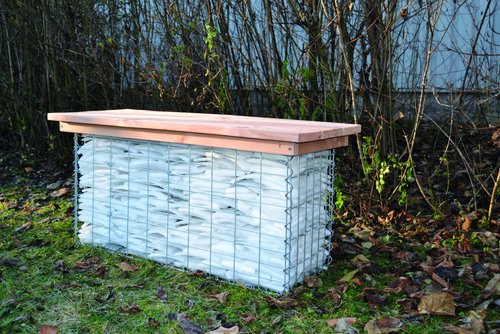
In the project the manufacturing processes and products along the entire added-value chain, from the production of silicon mono-crystals to sawing the wafers, the production of solar cells and modules through to the recycling of by-products and modules, were optimised to consume the lowest possible energy and resources and to save costs.
Working in close cooperation with ten international project partners: Sintef Materials and Chemistry (coordinator, Norway), Norsun AS (Norway), UAB Soli Tek R&D (Lithuania), International Solar Energy Research Center Konstanz (Germany), Apollon Solar (France), Garbo Srl (Italy), Boukje.com Consulting BV (Netherlands), Asociacion de Investigacion Metalurgica del Noroeste (Spain), Steuler Solar Technology AS (Norway) and Inesea Automation SL (Spain), the respective environmental effects of the individual process steps were examined at the bifa Umweltinstitut. For comparison, the status of the production of so-called standard modules was examined in a life cycle and eco-efficiency analysis at the start of the project, at the project half-time and at the end of the project.
Many of the project objectives were fully achieved, and some were even exceeded:
- Recycling of argon in the melting furnace for the silicon
- Development of reusable moulds for the silicon crystallisation
- Recycling of saw particles
- Recirculation of the water used in solar cell production
- Reducing silver consumption in solar cell production
- Development of new frameless and glass-glass solar modules, dispensing with encapsulation materials made of plastic
- Simplification of recycling and
- Possibility of repairing solar cells (cell doctor) and modules
The argon recycling system has already been introduced successfully in production; repeated use of the ceramics was successfully demonstrated in the laboratory. New solar cell types allow far fewer quantities of silver to be used, whereby the consumption of ultra-pure water in cell production was successfully reduced. The dispensing with aluminium frames and encapsulation materials was demonstrated successfully; small quantities of polymers are still needed to fix the solar cells in the module, for edge sealing and for the junction box. The targeted saving of silicon through further reduction of the sawing wire thicknesses and the changeover to even thinner wafers is expected in the near future.
Furthermore, working in close cooperation with its partners, bifa is examining the recycling of by-products and waste such as quartz from the crucibles and moulds for decorative applications such as gabions, graphite from the furnace, the recycling and recovery routes of the solar cells, the glass and the complete modules. To this end, new chemical recipes for cleaning the solar cells and the glass were developed and methods for separating the modules by means of cutting and flashing light technology were tested.
Eco-Solar Factory was a three-year project with a budget of 5.64 million euros, which was fully implemented through the Horizon 2020 research and innovation programme of the European Union under the project ID 679692.
More at: http://ecosolar.eu.com