ForCycle II - Securing and retaining raw materials by treating and recovering dust from foundries
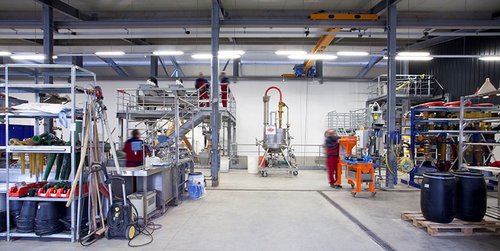
Augsburg, 28 August, 2019
Start of a research project involving Augsburg University, bifa Umweltinstitut, four Bavarian foundries and two specialists for treatment technologies.
The topic of resource efficiency is highly relevant for the Bavarian economy, as it is very highly integrated into the international raw materials markets and would also like to continue to produce economically and in an environmentally friendly way in its locations in the long term. A modern, sustainable resource strategy is not only targeted at the start of the raw material chain (access, criticality), but it also links to the end of the material chain (residual materials, waste) to form closed recycling processes.
Prof. Dr. Richard Weihrich (MRM Institute of Augsburg University) and Prof. Dr. Wolfgang Rommel (bifa) are working together with Bavarian foundries and suppliers on a research project, to close the material cycles in metalworking. The Bavarian foundries, more than 30 large and 60 smaller ones, are a key industry for the backbone of the Bavarian economy, from precision mechanics through to the vehicle and machinery industry. The project is being funded by the Bavarian State Ministry of the Environment and Consumer Protection (Bayerisches Staatsministerium für Umwelt und Verbraucherschutz).
Every second German company already uses recycled materials. A resource strategy uniformly supported by industry and the state is particularly useful. An essential aspect of being able to provide even more high-quality basic raw materials for the domestic production industry in the future is to add it to an efficient circular economy.
The foundry industry plays an important role in metal recycling. Steel, cast iron and aluminium scrap is remelted here to form new products. Despite large fractions containing recoverable materials, there are currently no or only inadequate recycling solutions for many of the types of dust separated out in the flue gas cleaning of foundries.
Just like in other branches of industry, the way to more environmentally friendly production and greater resource efficiency for the Bavarian foundries is a highly topical and important topic. Measures are required for increased reduction, recovery and reuse of waste. The economy of such a process is based on the saving of disposal costs and on recovering the materials contained in the residual materials as raw material substitutes.
The objective of the project is to examine economical and environmentally friendly alternatives to the disposal practices implemented to date. The topic is being worked on by a project group including the University of Augsburg and bifa Umweltinstitut GmbH, together with four southern German foundries and manufacturers of treatment technologies. The intention is to develop and implement practical ways of recovering, using and recycling metal dust for Bavarian foundries. In this way, important resources for the Bavarian economy remain in the material cycle.
The project partners are the University of Augsburg, bifa Umweltinstitut GmbH and the following Bavarian foundries: Franken Guss Kitzingen GmbH Co. KG, Gießerei Heunisch GmbH, Kemptner Eisengießerei Adam Hönig AG and Trompetter Guss GmbH Co. KG, as well as the SMEs AKW Apparate+Verfahren GmbH and GPS SIC Keßl GmbH u. Co. KG.
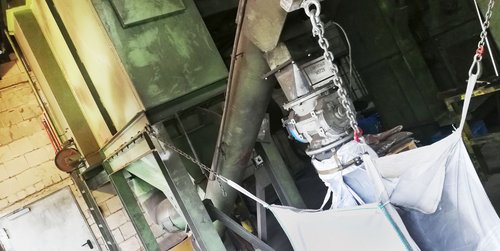