Metal dust recycling - ForCYCLE II: University of Augsburg cooperates with ECOMET Urban Metals
Augsburg, 18. November 2020
Recycling metal dust from foundries is the objective of a project at the University of Augsburg. To this end, the Institute for Materials Resource Management and its project partner, bifa Umweltinstitut GmbH, entered into a cooperation with the industrial company, Ecomet Urban Metals. The project is part of the ForCYCLE II project group for greater resource efficiency in Bavarian industry and is funded by the Bavarian State Ministry of the Environment and Consumer Protection.
Wherever metal is cast and machined, harmful metal dust gets into the air. Efficient extraction of such dusts is indispensable, but poses a challenge for the processing firms that have to dispose of it. Until now, no recycling methods that are suitable for comprehensive recovery of the dusts have established themselves, instead the dusts mostly end up in land fill sites or as is used as mine filler. This is not only an environmental problem, but also entails high costs for the foundries. In addition, valuable elements and compounds are lost with the metal dust. Recycling it to make it usable for industrial applications protects the environment and allows new raw material cycles to be created.
The project: “Securing and Safeguarding Raw Materials through the Treatment and Recovery of Foundry Dusts – Bavarian Consortium for Foundry Dust-Metal Recovery – BGMR” is searching for viable solutions for metal dust recycling. The research partners are the Institute for Materials Resource Management of the University of Augsburg, bifa Umweltinstitut – one of the leading application-orientated research, development and consulting facilities in Germany – and in addition to six other partners in industry, the newly added partner Ecomet Urban Metals. The industrial company has developed a concept for producing high-quality metals and alloys from used metals, scrap and metal dust and makes this production method available to the scientists.
New alloys made of metal dust
“Due to the enormously high temperature of our plasma furnaces and the concentrated distribution of this heat in the melting process, we can produce new alloys from the metal dust. In one melting process, waste that is harmful to the environment and to health can thus be used to create new and high-quality alloys, which can be made directly re-accessible to all applications”, explained Giorgio Karhausen, Chairman of Ecomet Urban Metals.
“The problem mainly lies in the highly variable dust compositions, depending on the foundry and where the dust is produced. In addition, the dusts contain very many different compounds and elements. This makes their return into existing recycling routes significantly more difficult. The dusts have until now eluded the cycle economy concept, the usual metal disposal and recycling routes cannot be used for them. Through this project, we want to show the possibilities that exist for continued (re)use of metal dusts and the raw material added value that can be created as a result”, said Prof. Dr. Richard Weihrich, who heads the project at the Institute for Materials Resource Management.
Professor Dr.-Ing. Wolfgang Rommel, Managing Director of bifa Umweltinstitut, emphasised: “The objective of the project is, in cooperation with companies, to develop and realise practical ways for the recovery, use and recycling of metal dusts from Bavarian foundries and in this way, to keep important resources available to industry in the material cycle. This increases resource efficiency in key industries, secures resources previously lost, reduces the impact on the environment and increases profitability.”
Fewer transport movements
The advantage of the tested method, said Karhausen, is that foundry dust can be recycled in its direct form without needing other processes. “In this way we make it possible for foundries to achieve disposal far more efficiently. Our goal is, where possible, to produce locally where sufficient quantities of raw materials arise, instead of having to transport them around the world first. This reduces waste and scrap tourism.” Decentralised production also reduces dependencies of the processing industry, which have again become a risk, among other things due to re-emerging trading and customs conflicts.
The project partners in the collaborative project within the scope of the ForCYCLE II project group are:
Universität Augsburg, bifa Umweltinstitut GmbH and the following Bavarian foundries: Franken Guss Kitzingen GmbH Co. KG, Gießerei Heunisch GmbH, Kemptener Eisengießerei Adam Hönig AG und Trompetter Guss GmbH Co. KG, as the KMUs AKW Apparate+Verfahren GmbH and GPS SIC Keßl GmbH u. Co. KG and ECOMET Urban Metals AG
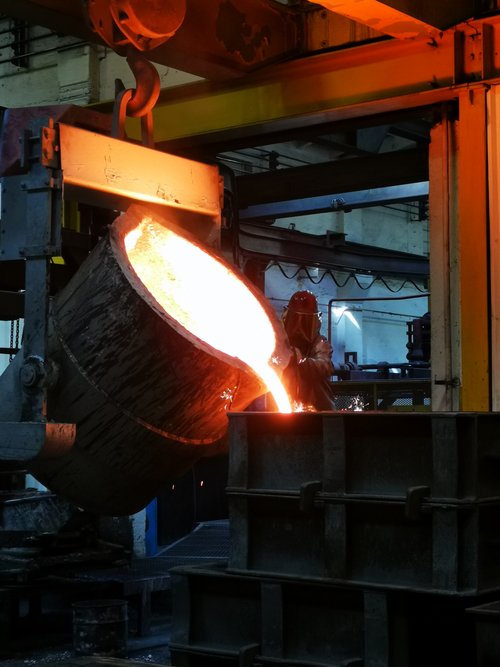