Using foundry dust as a secondary raw material
In the previous project, which was part of the ForCycle II project network, recycling options were defined for dusts from Bavarian foundries in order to return them to the material cycle in a sustainable way.
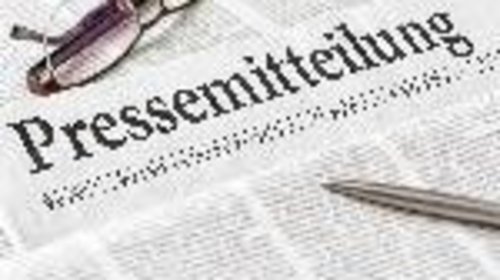
The current project, foundry dust recycling in the pilot plant and application, is part of the ForCYCLE pilot plant project network and aims to recycle process dusts from foundries that accumulate in quantities of several hundred tonnes per year. The project will transfer the precise mapping, classification and digitisation of the dusts, which began in ForCycle II, as well as laboratory tests, to the pilot plant scale. Previously, only primary raw materials were used to produce foundry aggregates. Dusts can serve as secondary sources of quartz and metals and can be processed complete with all their components.
One focus is on optimising the pellets, considering alternative CO2-minimised binders, digitally supported recipes and adjusting the basicity of the pellets. Eco-efficiency and CO2 balance are recorded and optimised using a life cycle assessment. At the bifa environmental institute, the composition of dusts produced in the foundry is analysed. These data are essential for creating recipes for briquetting tests. Together with Franken Guss GmbH & Co. KG, recipe variants for pressed parts are to be systematically developed from digitised dust data, which will then be used again as additives for the foundries.
First briquetting tests successfully completed
The knowledge gained from the preliminary laboratory-scale tests is being used to technically implement the processes for manufacturing the moulds with the addition of dusts at GPS Sic Keßl GmbH u. Co. KG.
The first small series to be produced was SiC/Mn green bricks for a partner foundry. The specification of the recipe for these green bricks was adapted to include the dusts. Possible recipes had already been identified in advance in laboratory tests. In the first series of tests, green bricks were produced with different mixing ratios of the defined dusts.
No disadvantages resulted from the addition of the dusts, either during mixing or during subsequent processing on the multi-layer paver. The immediate strength of the moulded parts was sufficient to allow them to be stacked on top of each other immediately after processing. The test moulded parts were removed from the standard mould after two days and sealed in film.
The strengths of the samples are determined in comparison to the normal series samples.
Digitisation for transferability to other foundries and integration into life cycle assessment
Databases are to be built using the digital data obtained. These will enable the development of intelligent algorithms that combine dust fractions as needed. This will also allow the digitisation of various scenarios of resource use and processing in foundries.
The GiTe project is part of the ForCYCLE – Technikum project network, which is financed by the Bavarian State Ministry of the Environment and Consumer Protection (STMUV) and coordinated by the Resource Efficiency Centre (REZ) at the Bavarian State Office for the Environment (LfU). The project partners are bifa Umweltinstitut GmbH, Franken Guss Co. KG, GPS SIC Keßl GmbH & Co. KG and the University of Augsburg (Institute for Materials Resource Management).
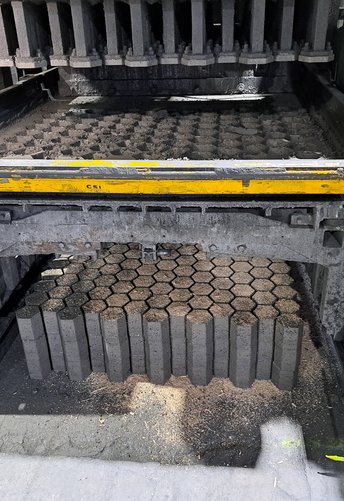