iuta e.V.: Process optimising corrosion protection concepts in incineration plants
There are limits to the high efficiency of power generation by waste incineration, because the temperature of the superheated steam is generally limited to around 400°C to protect against corrosion damage.
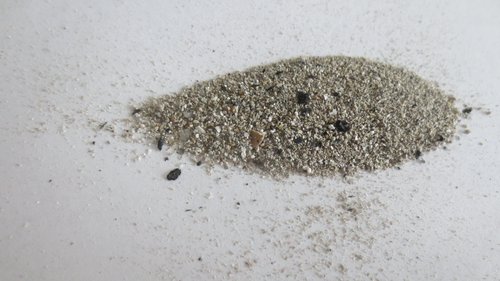
The causes for the high-temperature corrosion in the area near the pipe wall are largely clear: The formation of deposits and reaction of deposited chlorides with the sulphur dioxide in the flue gas ensures chlorine replenishments in a cyclic process largely shielded from the atmosphere by the deposits. Unlike particles containing chloride, gaseous hydrogen chloride does not play a significant role.
bifa and IUTA were able to improve the quality of measurements of the corrosive particle phase significantly by combining tried and tested measurement technology (dilution probe) and new measurement technology (membrane probe). The material flow balance of an incineration plant shows that the results are plausible and are representative for operation of the plant.
By comparative measurements on a more highly corroding boiler and a less corroding boiler, differences were identified regarding the corrosive particles. With total concentration of chlorine compounds roughly the same overall, in the more highly corroding boiler the fraction of the chlorine load existed in the particles, while in the flue gas of the less corrosive boiler the fraction of gaseous hydrogen chloride was higher. Apparently, the conversion of the chlorine compounds contained in the fuel takes place differently in the two plants.
The basis for modelling the formation of the deposits was prepared in the form of reliable data on the composition of the flue gas aerosol, the particle size distribution and on changes in the boiler. The measurements in the area of the furnace extended the knowledge of how the particles were formed and the particle discharge from the burning bed.